TROCKNNER equipment is suitable for various sludge drying systems, such as municipal sludge and industrial sludge (papermaking, electroplating, chemical industry, leather, medical products, food sludge, etc.).
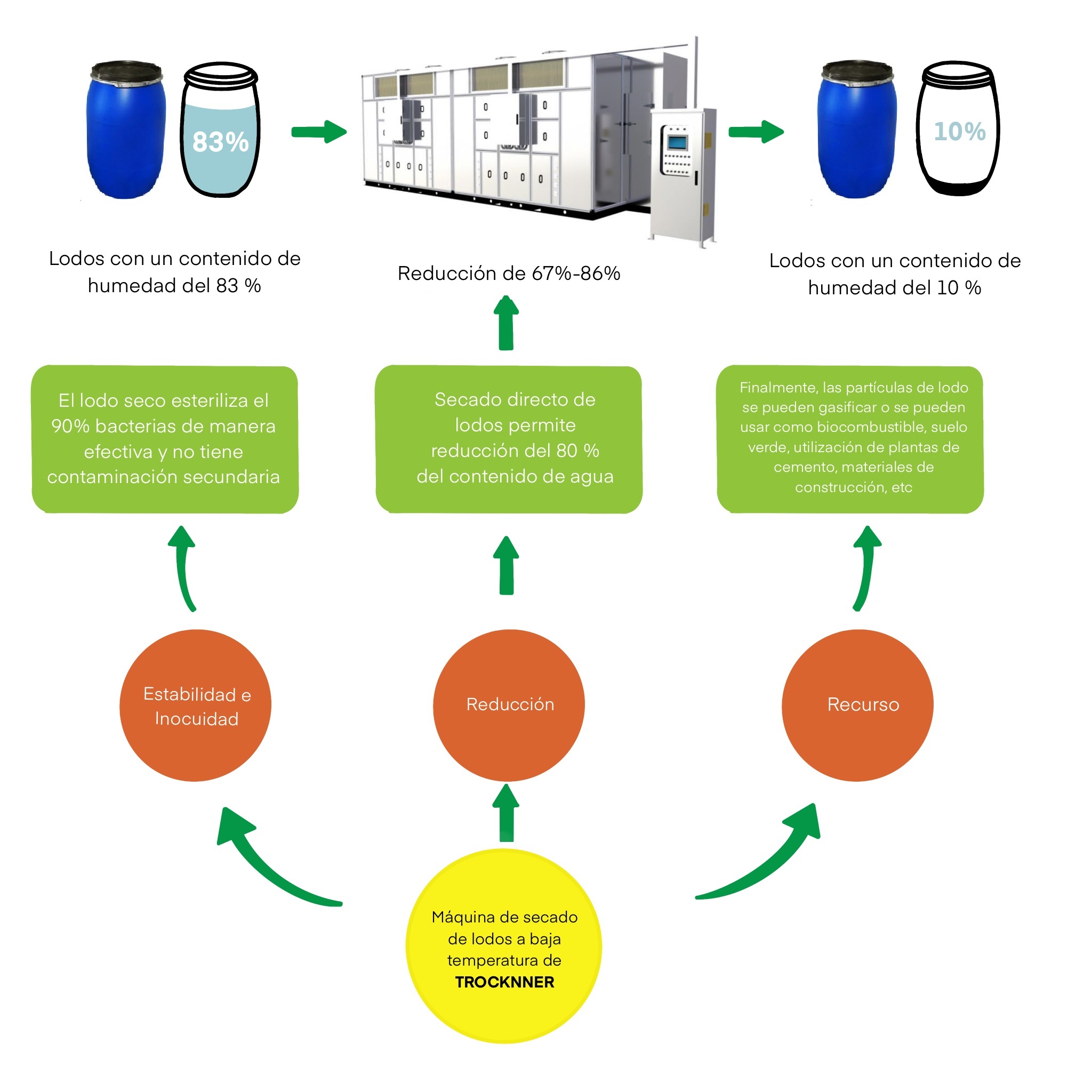

Sludge generally refers to the solid, water-containing sediment produced in the wastewater treatment process. Its material composition includes:
- Moisture content: Moisture content reaches 95% or more:
- Volatile substance and ash: The first is an organic impurity, the second is an inorganic impurity:
- Pathogens: Such as bacteria, viruses and parasite eggs, etc. These pathogens are abundant in sludges such as domestic wastewater, hospital wastewater, food industry wastewater, and tannery industry wastewater;
- Toxic substances: Such as cyanogen, mercury, chromium or some toxic organic substances that are difficult to decompose.
The main purposes of sludge treatment are as follows:
- First, to reduce the volume of the sludge, that is, to reduce the water content, with the aim of creating the conditions for the transportation, dewatering and comprehensive utilization of the sludge.
- The second is to make the mud stable. The sludge contains a large amount of organic matter, various pathogens and other harmful substances (such as heavy metals). If it is not stabilized, it will undoubtedly become a "secondary pollution source", resulting in environmental contamination and transmission of pathogens.
- The third is to improve the composition and some properties of the sludge through treatment, in order to facilitate the recycling of the sludge. In short, the principles of sludge treatment are reduction, stabilization, safety and recycling. In reduction and stabilization operations, the most important operation is to remove water from the sludge.
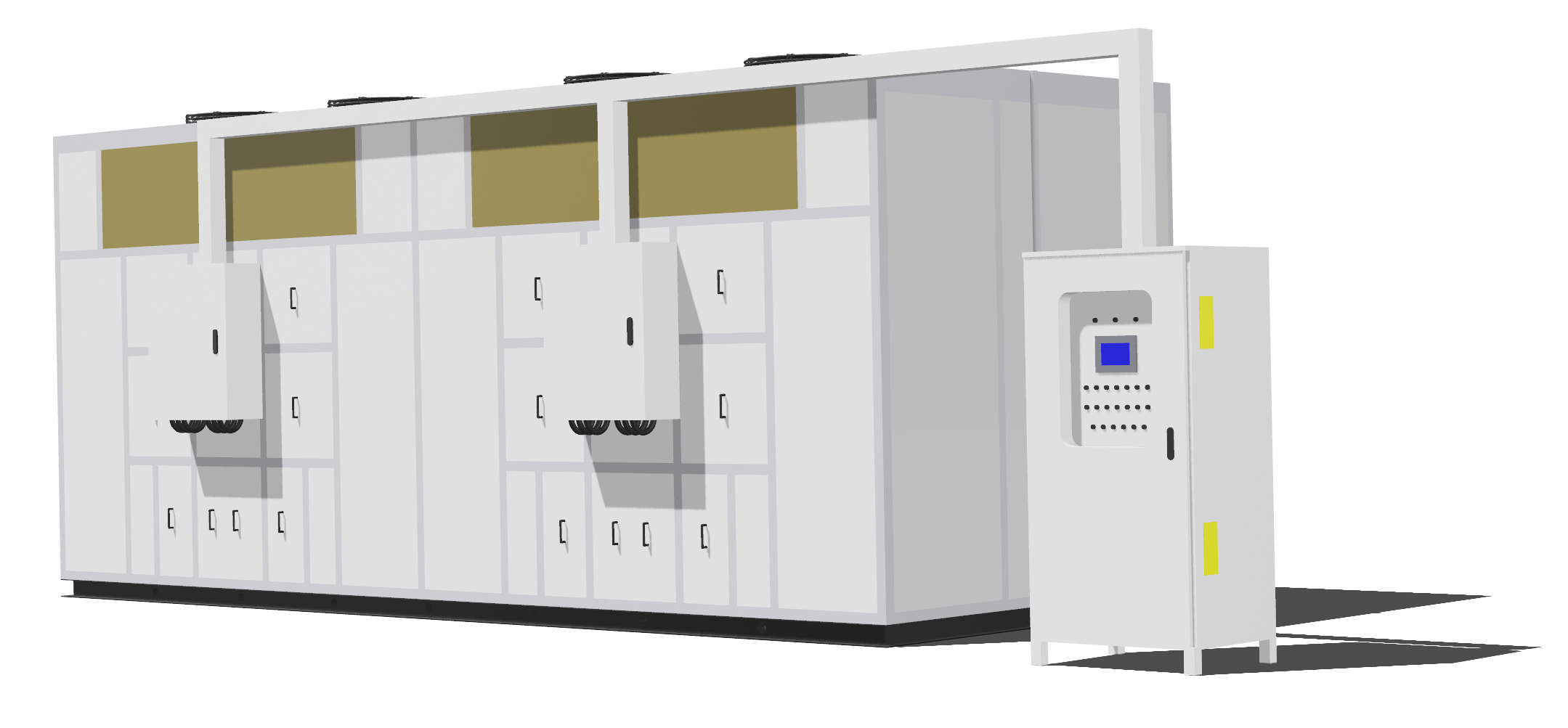
Operating principle
For drying sludge it is recommended to use a low temperature drying. The TROCKNNER heat pump is used to heat and dehumidify the air. The circulation of hot air through the product allows effective convection and mass exchange. Using the dry hot air, the moisture in the sludge absorbs heat from the air and evaporates in the air itself, becoming moist air which is then dehumidified and heat recovered to achieve the drying purposes and save energy. The refrigeration system is used to cool moist air below dew point to separate moisture, and the air is heated through multiple heat recovery technologies, so that moisture in the mud is evaporated all the time.
TROCKNNER sludge drying devices stand out for:
Security
- Low temperature drying process below 80°C is fully suitable for sludge drying.
- The system is safe to operate, there is no danger of explosion, it is not necessary to use nitrogen;
- The sludge has an oxygen content of <12%; dust concentration is 60 g/m² particle temperature is <70 °C;
- The mud is statically distributed and there is no mechanical static friction with the contact surface.
- In the non-municipal sludge drying process: The dried material is granular and there is no danger of dust;
- Low discharge temperature (50°C), no need for refrigeration, can be stored directly.
Environmental Protection
- Fully enclosed drying at low temperature. (40-80°C)
- It is not necessary to install a complex device to control odors, since in low temperature drying the precipitation of hydrogen sulfide and ammonia is greatly reduced.
- Suitable for installation in water treatment plants
- Condensing the water from the sludge becomes easier to handle (or directly), saving the cost of condensate treatment during the drying process.
Energy saving
- Using heat pump heat recovery technology, the closed drying mode has no waste heat discharge
- 80% of the wet sludge per ton is dried to 10%, and the total energy consumption is 210 kWh.
- 4.2 kilograms of water per degree of electricity (dehumidification performance ratio (SMER = 1:4.2 kg.H2O/kWh).
- 80% wet sludge per ton is 60% dry and total power consumption is 128kWh.
Efficient
- You can often directly dry 83-10% moisture sludge without segmentation (such as plate and frame pressure filtration + thermal drying, thin bed drying + band drying, etc.):
- There is no loss of organic components in the drying process, and the dry matter has a high calorific value, which is suitable for the subsequent use of the resource.
- Capacity reduced by 67% and weight reduced by 80%, which can save a lot of post-transportation costs.
- It can be used for drying sludge with 83 - 50% humidity.
Intelligent
- Fully automatic operation, saving a lot of labor cost;
- PLC based intelligent control + touch screen
- The discharge water content can be arbitrarily adjusted (10% - 50%)
Pioneering technology
- By adopting the patented four-effect dehumidification technology, the controllable air humidity is lower (up to 10%), the drying efficiency is faster, and a large amount of fan power consumption can be saved.
- Independent layered air system to meet the requirements of rapid dewatering of wet sludge, short cycle of low temperature drying.
- Modular structure design, strong load regulation, easy to install and convenient.
- The transmission and feeding motors adopt variable frequency stepless speed regulation, which is suitable for the adjustment of dry material with different water contents (10%-50%), and has strong adaptability and stability.
Stabilization
- Pasteur sterilization method: Low temperature heating sterilization, drying rate above 70°C for 90 min - 120 min, can effectively sterilize more than 96% of the product.
Small installation area
- It covers a small area on average about 4 feet per ton of mud.
- There is no complicated civil structure and infrastructure construction, and the cost of civil construction is saved.
- The installation of the equipment is simple and the installation period is short.
Durable
- Use of stainless steel and other materials, heat exchanger with materials of high resistance to corrosion and anti-corrosion arrangement of plates, granting a long useful life.
- There is no mechanical wear during operation, and the service life is more than 15 years.
- No fragile and wearable parts, easy to use and handle.
Wide application
- The daily treatment capacity of a single drying line can reach 100 tons, which is suitable for sludge dispersion or centralized treatment mode, saving sludge transportation costs and reducing environmental pollution during transportation. It can solve the problem of difficult disposal of municipal sludge.
- It is not affected by ambient temperature (low temperature in winter) and humidity (humidity in summer), so it is suitable for use in different regions.

Order process
INQUIRY → QUOTE → AGREEMENT → ORDER CONFIRMATION → DEPOSIT (60%) → PRODUCTION → BALANCE PAYMENT (40%) → INVOICE → DELIVERY → INSTALLATION → TRAINING
Payment service
Transfer
Cash
PayPal / AliPay
After-sales service
- Technical support for installation, operation and maintenance.
- One-year warranty, with the possibility of an extended warranty.
- Spare parts and technical support at lower prices after the warranty.
- Updates to the latest product information and adjustments.
- Discounts are available for existing customers.
Note: For more information visit → CONDITIONS OF SALE AND DELIVERY
Join the sustainability movement and make your business greener with our drying equipment.
Contact us today for more information!